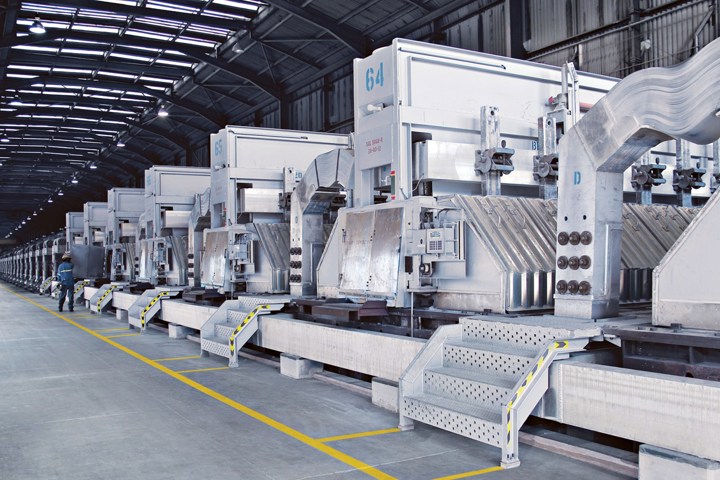
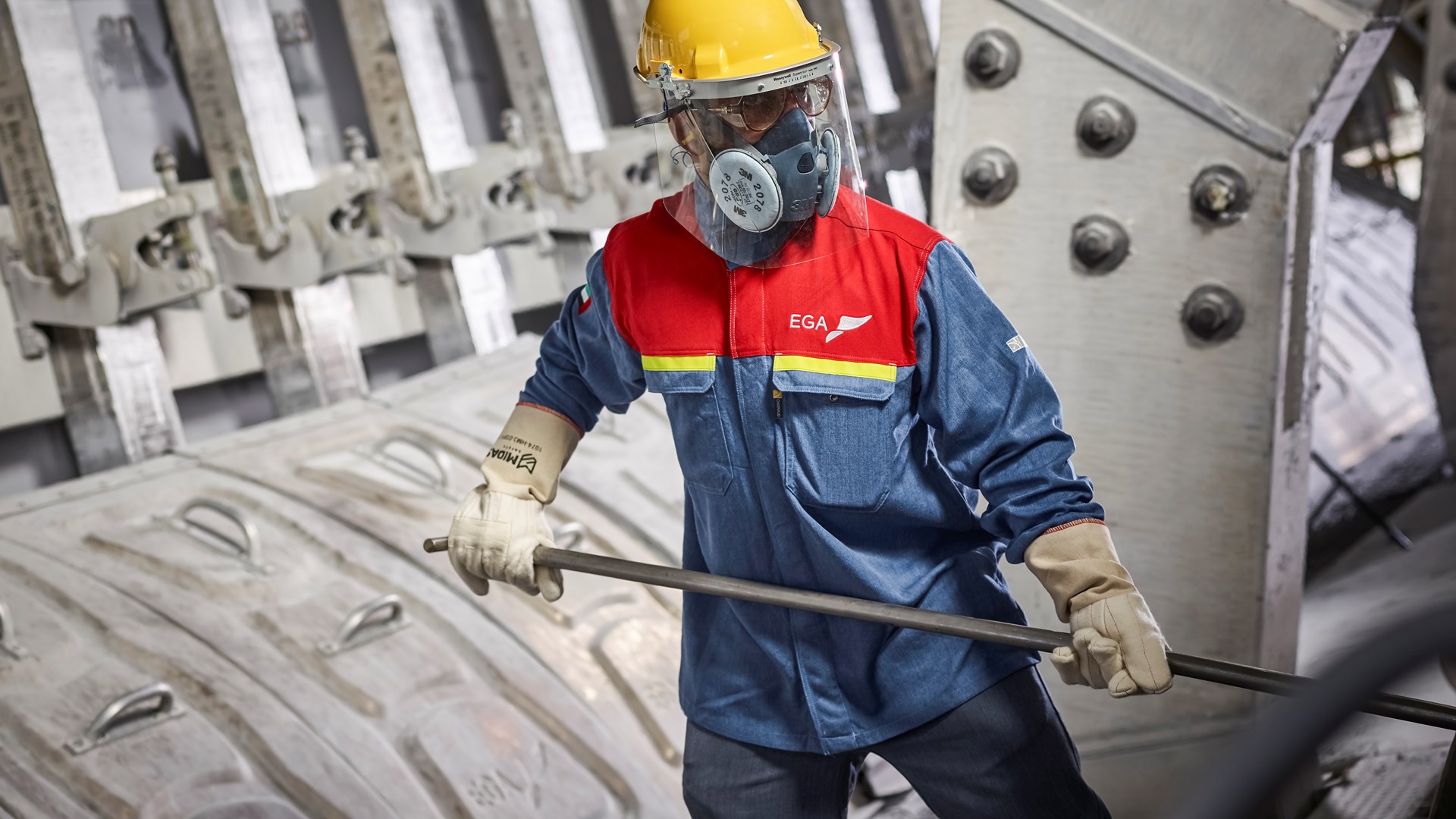
Eliminating the risk of harm
At Emirates Global Aluminium, we have a bold aspiration to eliminate the risk of harm from our operations and processes by 2030. We are focused both on physical harm, and on fostering mental wellbeing. This is a very challenging target which has never been achieved by any company before. We believe we have a responsibility to our current and future employees and contractors to strive to achieve it.
At EGA, we always put safety first. The only acceptable target is zero harm. We care for our people and our neighbours.
Safety is everyone’s responsibility at EGA. All our employees and contractors are able to identify and suggest methods to improve safety and have access to ways to raise safety concerns as part of our core policy, we emphasise that anyone and everyone at EGA has the authority to refuse or stop any activity perceived to be unsafe.
‘Beat the Heat’
Heat-related illness is a particularly significant hazard in the Gulf to people working outside in the summer. With climate change, it is becoming an increasing concern around the world. If left untreated, heat-related illness can even be fatal. EGA’s industrial processes cannot be switched off, meaning we work around the clock every day of the year.
We have focused on preventing heat-related illness for decades. In 2024, we achieved our goal of zero cases all summer.
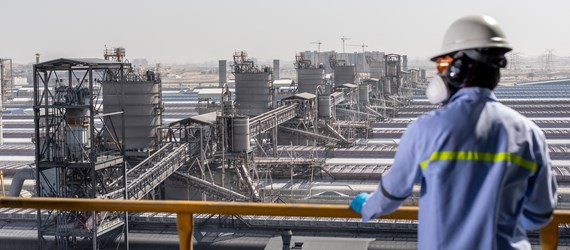
EGA’s ‘Beat the Heat’ programme is an intense, summer-long effort every year. We conduct hydration tests before and during shifts.
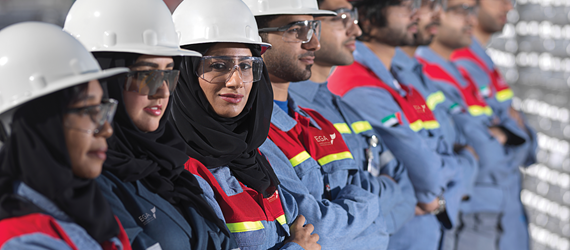
All employees working outside are trained in the early signs of heat-related illness and are empowered to act for themselves and others.
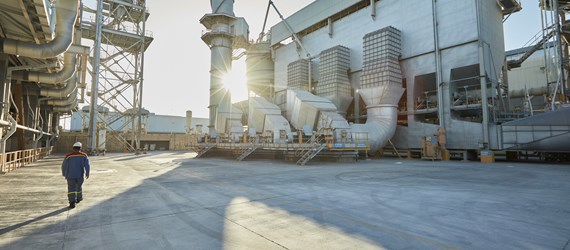
We run a hydration testing programme to ensure employees are fit for work both, before and during, their shifts.
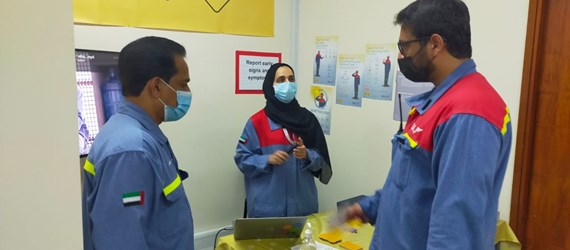
We have cooling booths, drinking stations, icemakers, and portable air conditioning units in our production areas to help employees stay cool.
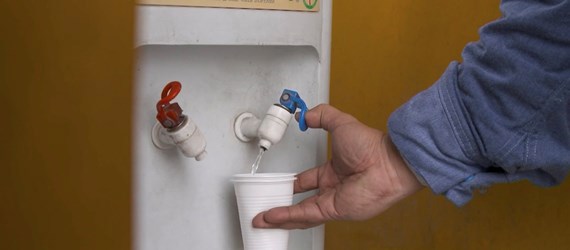
Our team members take regular breaks, and a lot of cooling showers. UV protection and heat rash prevention creams help keep people comfortable, and we have reusable water bottles and access to electrolyte drinks.
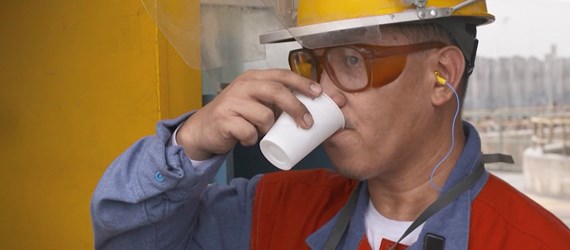
When an employee returns from vacation, they must go through an acclimatisation period, where they perform light then medium duty before returning to regular work.
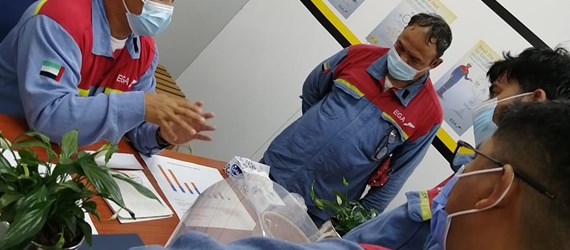
We investigate new technologies to make our ‘Beat the Heat’ programme even more effective, such as wearable devices to detect the early signs of heat-related illness before individuals even feel anything.
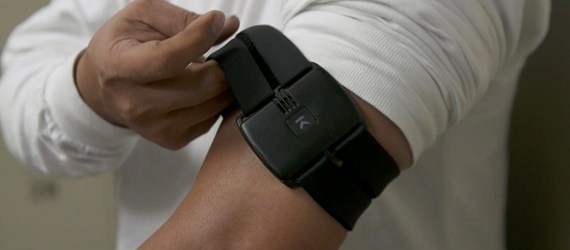
Watch this report from CNN about our latest improvements in how we ‘Beat the Heat’.
View original post on LinkedIn
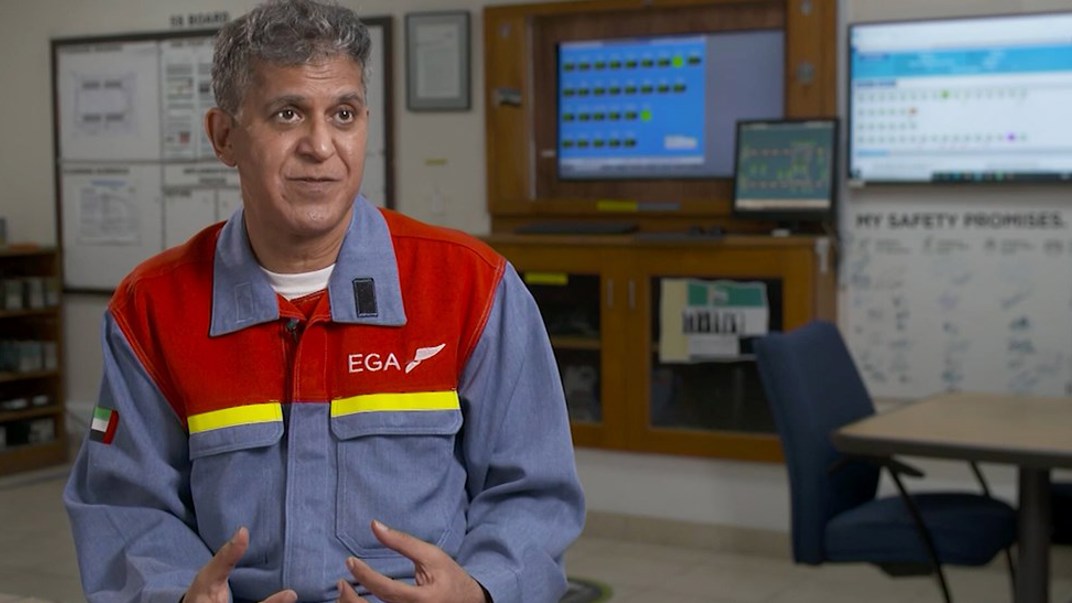